Process Optimization
Should you “Go up to 11?”
Increasing the blast pressure may produce desired results faster, or it may turn that beautiful matte finish into a cratered moon surface. Here’s what you need to know before you crank that pressure all the way up.
Velocity Relies on Blast Pressure
Particle velocity has a linear relationship with blast pressure. Increasing blast pressure pushes more air through to the nozzle. More air molecules in the stream increase the likelihood that those molecules will hit the back of an abrasive particle and push it through the tube faster.
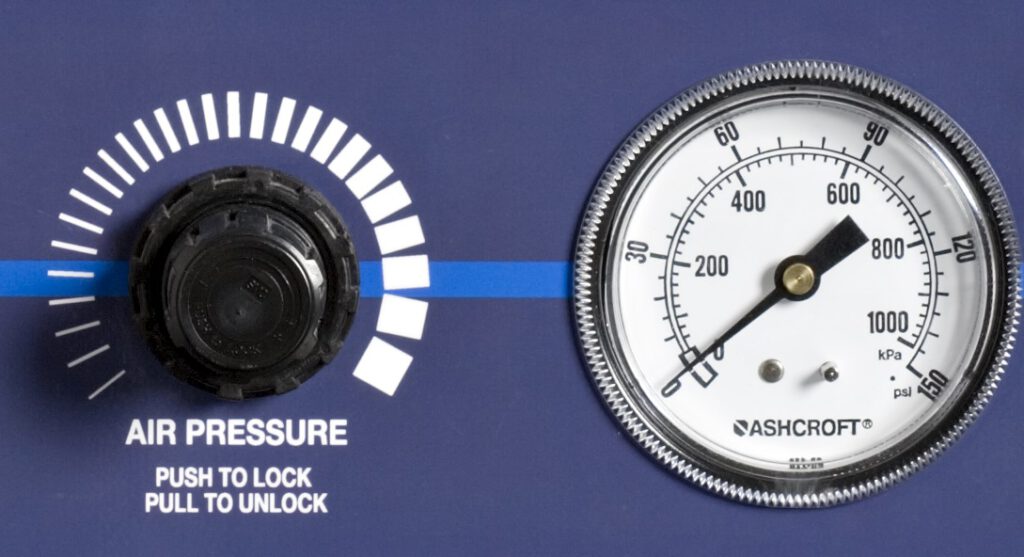
There are four core variables to MicroBlasting: abrasive size, type, and quantity, and particle velocity. Particle velocity determines how much energy each abrasive particle transfers to the surface. It is influenced by nozzle type, nozzle distance, the quantity of abrasive and most significantly, blast pressure.
Again, increasing blast pressure does not pump in more abrasive; it just pushes the abrasive through faster.
Higher blast pressure magnifies the end results that the abrasive particle imparts–be it roughening or cleaning a surface. Most applications have an upper threshold where the work crosses over from a positive to a negative impact. For instance, if the pressure is too high in conformal coating removal applications, then removal becomes uncontrollable and the solder mask may be stripped or damaged.
Setting the Pressure
Identifying and setting a blast pressure should be part of the R&D in the planning stages, and blast pressure should be tightly controlled throughout production to reduce risk.
Where to start?
- Our Applications Lab Technicians provide the ideal blast pressure with each Sample Parts Report. Our Tech Support Specialists are more than willing to provide guidance at any phase. Contact Tech Support at techsupport@comcoinc.com.
- If you are unsure and willing to gamble; start at 50 psi, and work from there. Most applications use an operating pressure in the 60-80 psi range.
- If you need to slightly increase or decrease Ra; then carefully make small adjustments to the blast pressure.
Important Note!
Keep the blast pressure at least 10 psi lower than the house pressure to prevent damage to your blaster. If the inlet air pressure is not at least 10 psi higher than the blast pressure OR there is a restriction in airflow; the dynamic air pressure may drop, decreasing particle velocity. Also, if the inlet air pressure drops below the blast pressure; the abrasive may migrate back through the machine, damaging critical components.
Learn more about how to prevent abrasive contamination.
Examples
Thermocouples
MicroBlasting is regularly used to remove a controlled amount of magnesium oxide MgO from tubes around wiring. The goal is to expose a specific length of the wires at a uniform depth. High pressure speeds the removal process, but use too high a pressure and create an uneven depth, which impacts the conductivity of the circuit.
Circuit Boards
Pressures that are too low lack enough energy to cut through the gummy conformal coating. Pressures that are too high cut past the coating and damage the solder mask (the green stuff in the picture to the left).
Solar Cell Edge Deletion
MicroBlasting quickly removes the CIGS layer without eroding the underlying glass or moly layer. Lower pressure is better because there is less risk to the underlying layer of glass or Molybdenum (Moly). Unfortunately, low pressure requires more time and more passes. The right system is key to this application. It should provide enough control over pressure and particle velocity to remove the entire layer in a single high-pressure pass.
Epoxy Removal on LEDs
This app requires high volume production. Higher pressures remove the epoxy faster; but can damage the protection device on the wafer, ruining the LED. One solution is to remove most of the material at a higher pressure and then sweep back at a lower pressure to make the final, more accurate cut.
Hose Length is Important
The biggest thief of air pressure is the abrasive hose. The media stream faces frictional loss as the air and abrasive travel from the blaster out to the nozzle, resulting in a pressure drop. In long sections of hose the effective pressure out at the nozzle may be just half of what is registered at the regulator; so adjust accordingly.
Keep your hose as short as possible, and replace it with the same length of the hose during maintenance. If the hose bursts or breaks do not cut the damaged section off and reattach the shorter hose. The shortened length will alter your results.
Machine Design Matters
Consistent abrasive flow is important for every application. Abrasive surges cause velocity to drop; making regulated blast pressure a less effective tool to control the process.
Comco’s MicroBlasting systems are specifically designed to feed a controlled amount of abrasive into the mixing chamber and out to the nozzle. This stable flow of abrasive leads to stable particle velocities, which leads to a consistent and repeatable surface finish.
Notes about Comco systems
Applications that require high air flow rates benefit from the internal geometry of large hose diameters (3/8″) on our DirectFlo™ and PowerFlo®. Large hoses create less frictional loss; so the pressure at the nozzle is closer to the pressure at the regulator.
Each of our Automated Systems features an electronic regulator that allows an engineer to set and adjust blast pressure at a program level; preventing fluctuation due to operator error.