Maintenance & Troubleshooting
Fight the Urge to Pedal Pump
Do you Pedal Pump?
Pedal pumping refers to the rapid pressing and releasing of a micro-abrasive blaster’s footswitch. It quickly starts and stops the abrasive stream, eliciting blasting intervals that last 2-4 seconds. Pedal pumping produces a brief, concentrated abrasive stream. It looks produces an abrasive stream that looks like this:
Operators tend to pump the footswitch for one of two reasons:
- Confusion about abrasive visibility.
- A need for a richer abrasive stream.
Unfortunately, pedal pumping is inefficient in both instances. Worse, it is really hard on your blaster. Let’s look at the consequences of pedal pumping and how to adjust your process.
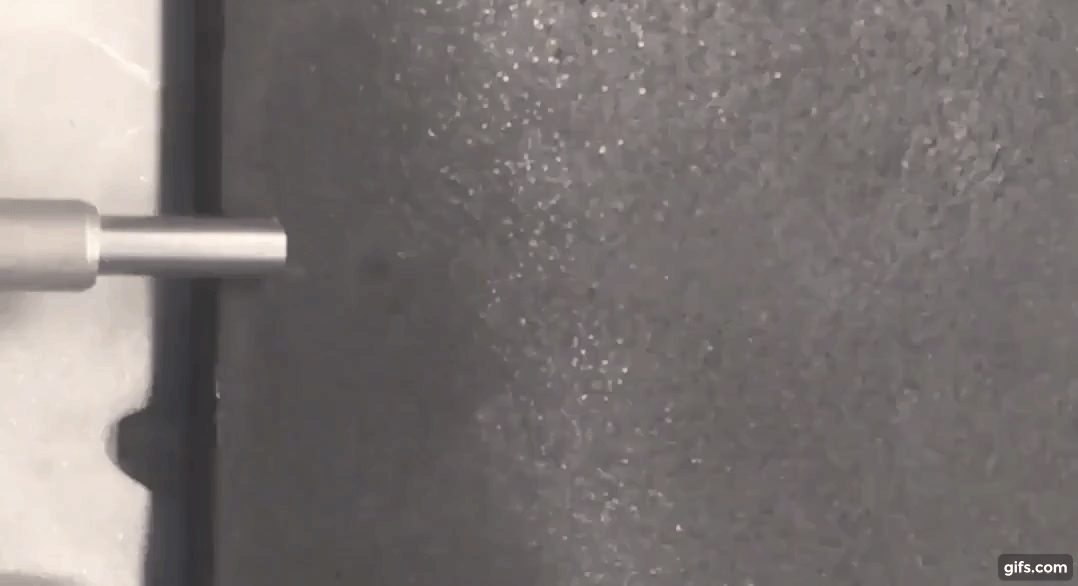
Like the Road Runner: You Should Not See Abrasive at Optimal Speed!
Operators often pump the pedal because they mistake their inability to see the abrasive stream with reduced abrasive flow or problems with the blaster.
Remember the old ‘Wile E. Coyote’ and ‘Road Runner’ chase scenes from Looney Tunes cartoons? The Road Runner was barely visible when it escaped at top speed. The Coyote only knew the bird was near because he heard its taunting “beep beep.” Rarely did the Coyote actually see Road Runner running past because that bird moved too fast.
Think of the abrasive stream like the Road Runner. The stream needs time to reach full acceleration, so abrasive particles are visible to the eye at the initial press of the footswitch. However, once the stream is up to its optimal speed of 150-250 meters per second, particles travel too fast to be seen.
Need a Rich Abrasive Stream?
Many cleaning and texturing applications benefit from a rich abrasive stream that pedal pumping provides. Rich abrasive streams tend to deliver rough and more thorough surface finishes quickly.
Pedal pumping burns through abrasive at a faster rate than a properly outfitted blaster running continuously at optimal speed. It wastes abrasive and delivers results that are not easily repeatable. If your application benefits from a rich abrasive stream, switch to a larger nozzle and use a larger abrasive tank orifice.
Need help selecting the right size tank orifice? Check out this guide.
Pumping Leads to Pile-Ups
In the experiment above, we blasted 4 holes in a glass slide using (L-R) 7 grams of abrasive per minute, 9 g/m, 25 g/m and 75 g/m. As you can see, the leanest abrasive stream delivered the deepest holes. All other variables in this experiment remained constant. We used a 0.046″ nozzle at 80 psi with the nozzle 0.100″ from the slide surface on all 4 holes.
A rich abrasive stream actually slows down the MicroBlasting process in hole-drilling applications. As a hole gets deeper, spent abrasive cannot move out of the incoming stream’s path fast enough. New abrasive strikes spent abrasive rather than the part surface.
Why is Pedal Pumping Hard on Your Blaster?
The pinch valve on the MicroBlaster® is rated to 10,000 cycles. The PowderGate® on the AccuFlo® is rated to 250,000 cycles. These may seem like long lifespans, but we have seen operators plow through 10,000 cycles per day in steady production due to pedal pumping. The opening and closing motions wear on this critical mechanism—be it a pinch or PowderGate—so speeding up that action just hastens their degradation.
How To Prevent Pumping?
The first step in solving this problem is education. Share this post with your operators. Make sure they understand the potential damage that pedal pumping causes and why it is counterproductive.
Again, if your application requires a rich abrasive stream, have the operators use a larger nozzle and a larger tank orifice.
Applications Lab
Let our experts help find the right solution for your part. We know no two applications are the same. Our Technical Specialists manage sample-part testing and processing from start-to-finish. They actively collaborate with our Sales and Engineering Teams while remaining completely accessible to you throughout the process.