Process Optimization
Have you Considered Pumice?
What makes Pumice a Great Abrasive?
- Comes from volcanoes!
- A tight particle classification.
- A gentle cutting abrasive—slightly harder than crushed glass and softer than aluminum oxide.
- Deburrs and textures metals precisely.
- Did we mention it comes from volcanoes? (Volcanoes are cool.)
Let’s take a look at this oft-forgotten media…
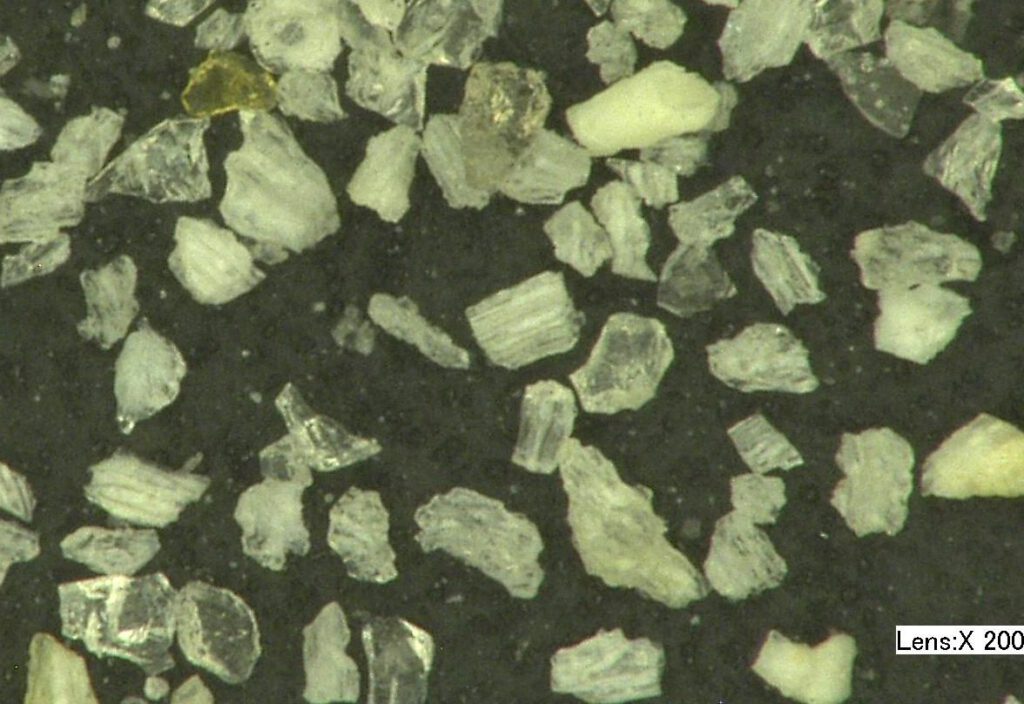
Tight Particle Classification
As you can see in the particle size distribution analysis above, about 3% of our pumice is larger than 177.95 µm, 50% > 82.09 µm, and 94% > 34.95 µm. In the past, we offered a pumice with more variance in particle sizing. Our new pumice has a really tight particle classification, so it delivers consistent results.
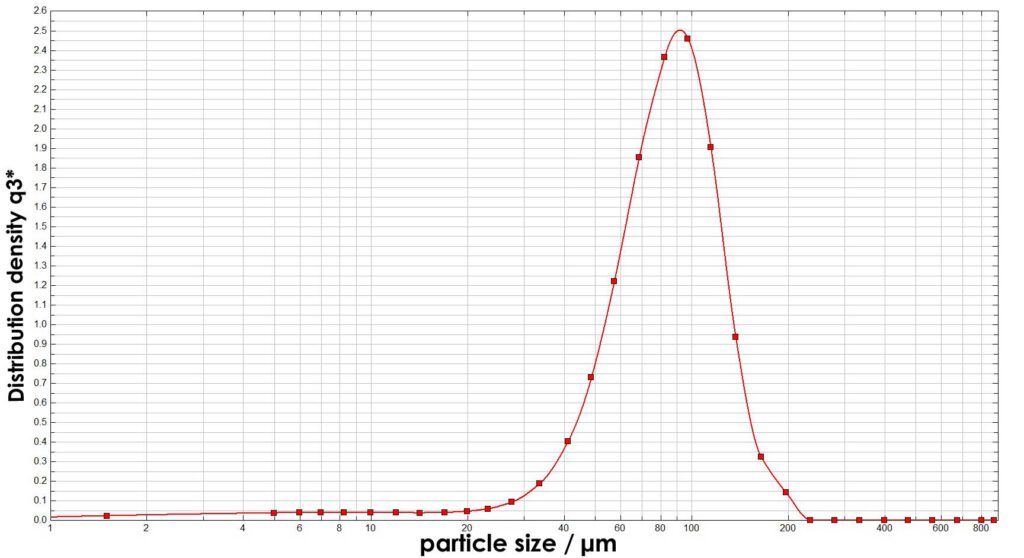
A Little Rougher Than Crushed Glass
If you tried crushed glass in the past and it was too gentle or produced muddy results, try pumice. Like crushed glass, pumice has a blocky shape with sharp edges and is silicon dioxide-based. It is harder and a little more abrasive. (It’s a 6 on the Mohs scale, while crushed glass is a 5.) It flows better than crushed glass and leaves a nice, matte finish.
Pumice Deburrs Metals
Pumice deserves more recognition as a great deburring agent. Aluminum oxide is the go-to deburring abrasive, but pumice has larger particles. (The larger the particle: the quicker it chops off burrs.) Pumice also has a softer impact than aluminum oxide, reducing risk to the underlying metal surface. In house, we refer to pumice as “AlOx- light.”
Quick Case Study: Bone Screws
Fine feather burrs often emerge on bone screws during machining. Large rollover burrs also erupt on a screw edges. MicroBlasting with sodium bicarbonate often removes both types of burrs; however, sometimes a more aggressive cutting abrasive is necessary.
Unfortunately, most cutting abrasives are too sharp and/or too hard for bone screws. Their particles dig past the burr and into the screw surface layer. Most cutting abrasives tend to leave a rough surface finish which increases drag.
Pumice is an ideal abrasive for blasting bone screws because it is a gentle cutting abrasive. Its particles are hard enough to break off stubborn burrs quickly but soft enough that they cannot significantly alter the surface of a bone screw underneath.
Remember, too, that MicroBlasting provides pinpoint precision which presents less risk overall to micro-features on small machined parts. Areas on a bone screw that do not require refinement can remain untouched.
Quick Case Study: Titanium Bone Plates
Much like bone screws, machining causes fine feather burrs to form on bone plates. These burrs must be removed before implantation in a human body. MicroBlasting allows an operator to selectively target areas on a bone plate, rather than exposing the entire part to abrasive. Plus, MicroBlasting reduces the risks presented when deburring with a knife or pick.
Crushed glass or glass bead are often used for this application, but pumice offers a few distinct advantages.
- Its particle sizing is more consistent than crushed glass, which means a more consistent flow of abrasive.
- Crushed glass has a wider distribution and can rat-hole in a tank or clump together.
- Glass bead is a peening abrasive, which means it can smear the edges, creating a lip if the blast pressure is too high or the operator blasts a single location too long.
- Glass bead leaves a satin finish, while pumice leaves a preferred matte.
Quickest Case Study: Drill Bits
Drill bits face the same deburring challenge and approach as bone plates and bone screws. Though it is worth noting that while pumice is a gentler abrasive than aluminum oxide, a pumice particle is still too angular to simply roll over the edge of a cutting feature. It is sharp enough to knock off burrs, but not so sharp that it dulls edges on a bit.