Abrasive
Jet Machining
with MicroBlasting
Micro-abrasive blasting is powerful enough to drill holes in ceramic substrates, yet gentle enough to cut slots in fragile silicon and glass wafers. MicroBlasting is “shockless,” generating neither heat nor vibration.
Unfamiliar
with
jet
machining?
Hydrodynamic Seals
Etch shallow channels into the groves or channels of the surface of a seal to crate an air bearing.
Thermocouples
Remove MgO to expose contacts for bonding on heat-sensing harnesses.
Microfluidics
Machine vias in glass and silicon to create through holes for MEMS devices.
Lens Engraving
Etch serial numbers into lenses for ring laser gyros without creating micro-cracks. rn

How to create features of a specific depth
A single pass of the focused abrasive stream from a MicroBlaster can uniformly remove 5 µin (0.127 microns) or less of material depending on the substrate, abrasive, and blast parameters. Given this level of precise and controllable erosion, you simply need to know how to fine-tune the process to suit your application.
Read more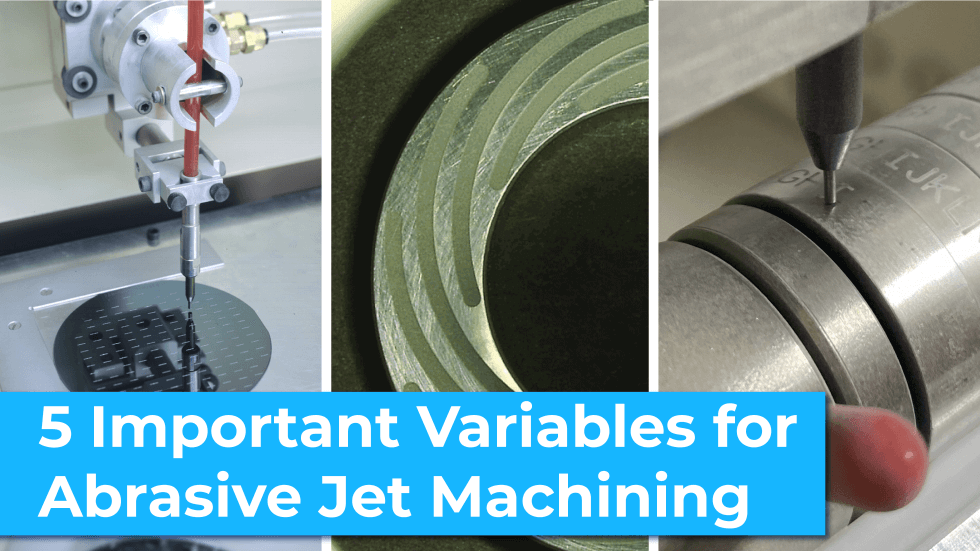
5 variables for abrasive jet machining
Using MicroBlasting to cut or etch a part (a process also known as controlled erosion) is a great method to machine many precision parts, from drilling holes in ceramic substrates to cutting slots in fragile silicon and glass wafers. MicroBlasting is “shockless,” generating neither heat nor vibration, meaning microcracks are less likely to form and damage part integrity.
Read more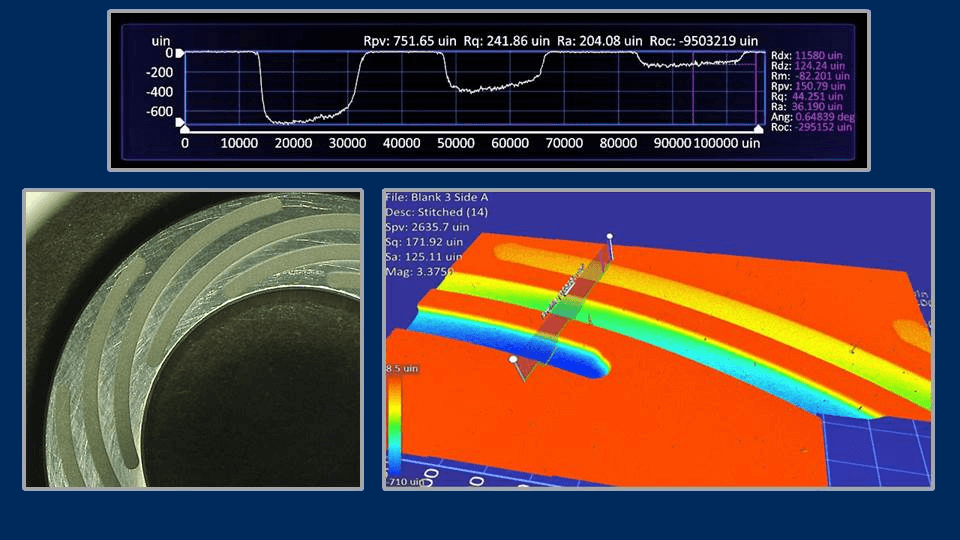
Etching channels to create an air bearing or hydrodynamic seal
Bearings inside turbine engines operate at high speeds in a harsh environment where traditional rolling contact or static bearings would not survive. To improve reliability and fuel efficiency specifically on jet engines, shallow channels are incorporated into the design in which air flows rather than traditional lubricants. The technical challenge is how to create these channels.
Read moreThe Manual System
The AccuFlo® produces a steady flow of abrasive which ensures consistent results. It processes parts faster than most traditional micro-abrasive blasters, and it does so with greater powder efficiency. The AccuFlo is able to handle a wide-range of abrasives and suits most MicroBlasting applications.
Learn moreAutomated Solutions
When a manual MicroBlasting system cannot provide the output or meet your tolerance requirements; Comco’s automated systems deliver all the benefits of a manual system with greater precision and efficiency. Both the Advanced Lathe and the JetCenter are designed for the steady processing of precision parts. Each automated system is customizable from a proven platform and delivered as a turnkey solution.
Learn moreWhy Choose Comco?
Do you know what sets a Comco micro-precision sandblaster apart from others? In short, It’s our modulator. This pulsing heart of our system transforms the technology from a dirt sprayer into a precision tool.
Learn more
MicroBlasting Capabilities Proven
-
An Experienced & Qualified Team
Engineers lead the process from concept to development. Our focus is on ensuring the process will work in production. We are as good at figuring out new applications as demonstrating what we have already done.
-
Our State-of-the-Art Lab
Our lab contains a complete range of MicroBlasting tools—from our manual stations to the fully programmable automated systems to run your samples. In addition, we have a complete inspection suite to document our results.
-
Comprehensive Results Ready for You
All results are captured in a clear and detailed report with pictures that you can take right back to your team along with the finished part.
-
Applied Engineering With a Deep Understanding of Industrial Manufacturing
Our engineers have a background in medical, aerospace, and the semiconductor industries. While we are experts at MicroBlasting, we can also “speak your language.”
TRY OUR PROCESS
See what precision MicroBlasting can do for you. Send us a part and we’ll MicroBlast it, analyze it, and return it to you with a detailed report.
Schedule a Demo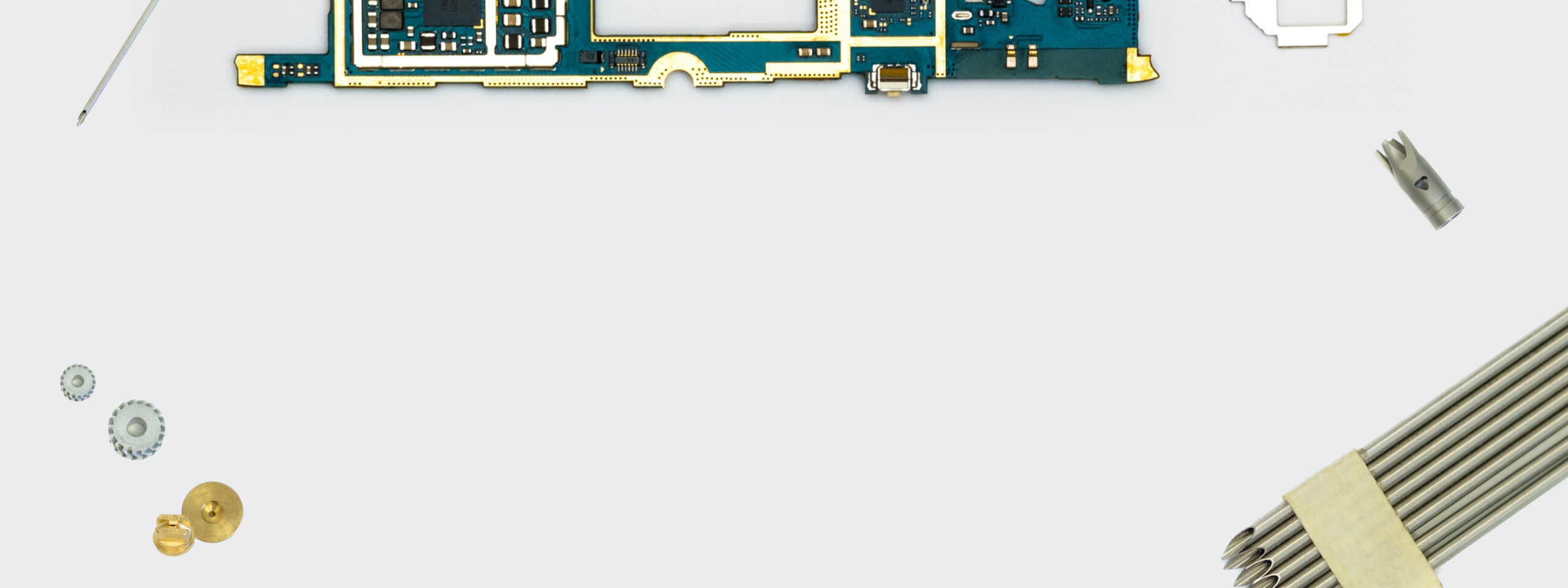