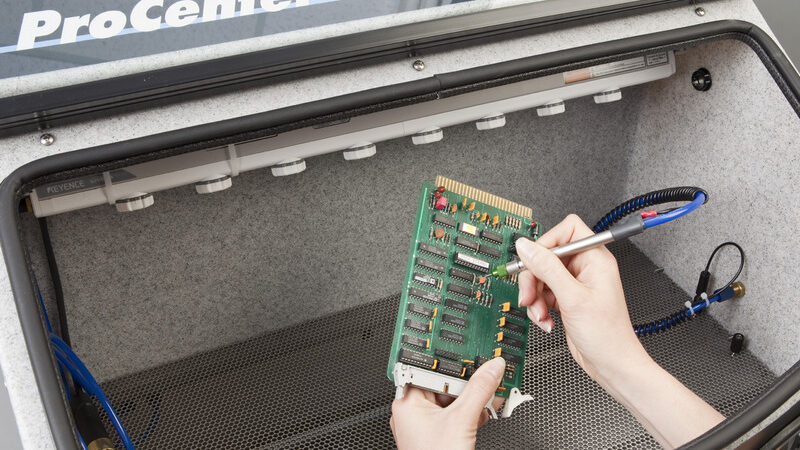
Conformal Coating Removal
Don’t risk the integrity of your circuit boards with heat and corrosive acids. Take control of your process with MicroBlasting. Your operators will thank you – it’s quick to master and safe to use without special protective equipment. The accountants will too – when compared to other conformal coating removal methods, MicroBlasting has been repeatedly found to be the fastest and most cost-effective.
Test Our Process on your partsHow Microblasting Works
MicroBlasting uses a very fine abrasive media mixed with compressed dry air. The precision nozzle gives the abrasive stream laser beam focus. By directing this stream at a shallow angle, the operator can easily peel off thin layers of coating. rn
Want to see this in action? Click the video.
Find the Right Abrasive for Your Coating
50
Walnut Shell
60
70
Walnut Shell
Wheat Starch
30
Plastic
50
Plastic
-
Wheat Starch
Wheat starch is the softest abrasive available for conformal coating removal applications. It has soft particles with shard-like edges, which make it excellent for abrading thin, pliable coatings like parylene and acrylic.
-
Plastic Media
Plastic media is a gentle abrasive and works well against the broadest range of coatings. It is the utility player of conformal coating removal abrasives. It quickly removes parylene and thick coatings. It is slightly harder than wheat starch, and its particles are smaller than walnut shell. Plastic media is treated to reduce electrostatic discharge.
-
Walnut Shell
If plastic media is not aggressive enough, try walnut shell. This is still one of our soft abrasives, so it is forgiving of operator error. But it features a slightly larger particle size with slightly sharper edges, which gives it greater cutting power.
-
Sodium Bicarbonate
If plastic media is not aggressive enough, try walnut shell. This is still one of our soft abrasives, so it is forgiving of operator error. But it features a slightly larger particle size with slightly sharper edges, which gives it greater cutting power.
Your Boss wants proof. WE can provide it.
Test Our Process on your parts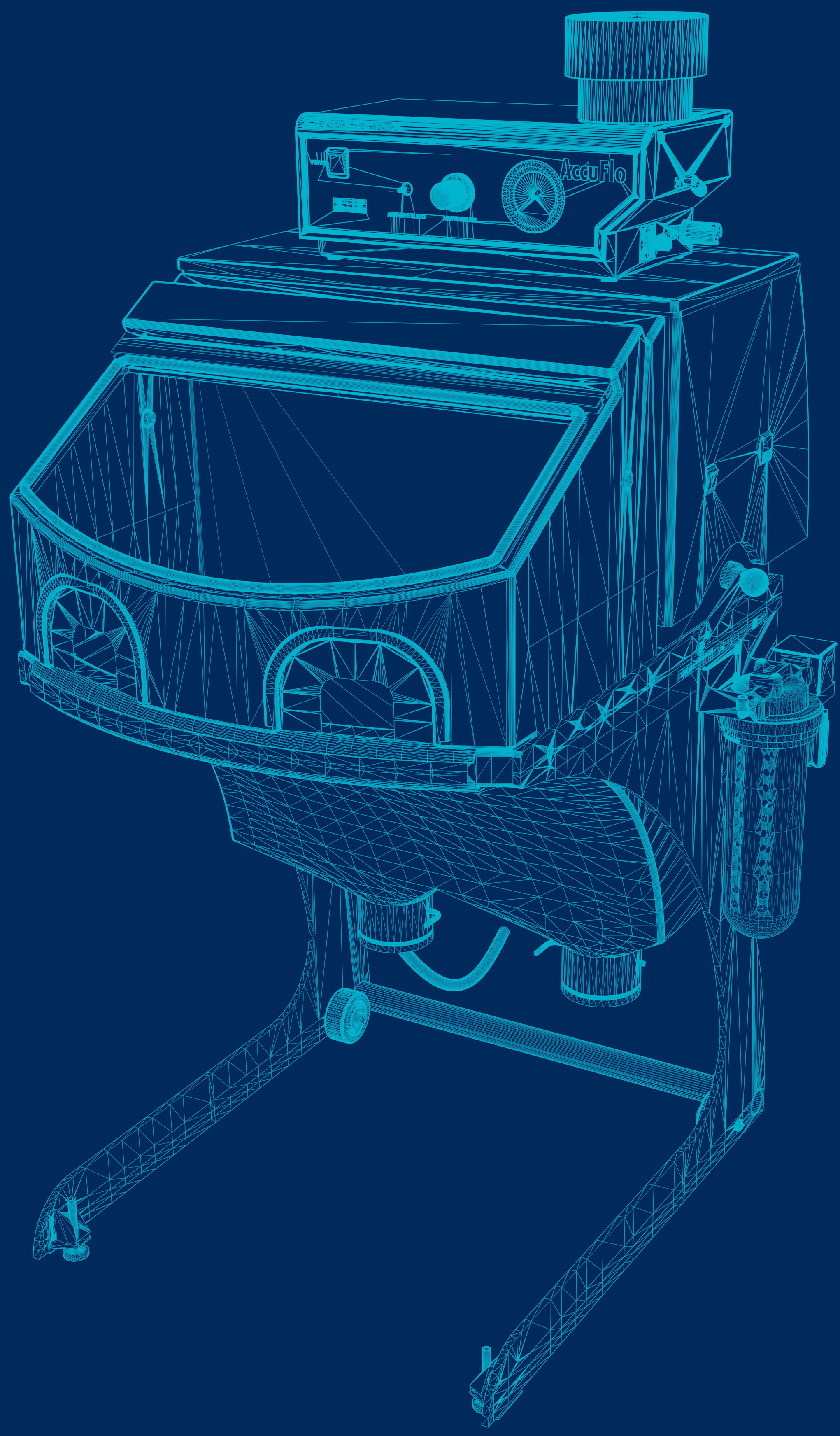
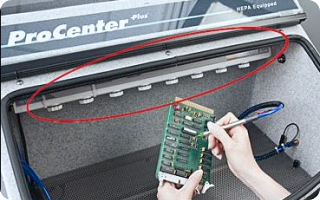
The Ionizer Bar
Floods the entire work chamber with ionized air to neutralize static build-up. Built-in sensors monitor the effectiveness of the ion flow and indicator lights alert the operator to any changes in operation.

Grounded Handpiece
Works with the conductive nozzle to provide a conduit for static, sending it straight to the grounding jacks instead of onto a PCB.

Conductive Nozzle
Limits the potential for a charge to travel to the board from the abrasive hose. A conductive nozzle also blocks a charge that could arc from the operator. Should be used with the grounded handpiece.
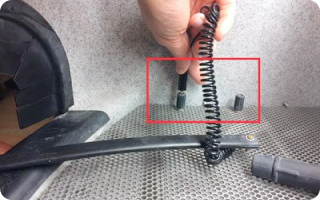
Grounding Jacks
Provide convenient connection points for a wrist-stat, the edge grounding bar, and the needle probe.

Edge Conductor Grounding Bar
Grounds all edge pins on boards that have edge connectors. This bar is made of conductive rubber material and connects to a grounding jack on the floor of the ProCenter Plus.

Needle Probe
Pierces through the coating and grounds a target trace when the defect is known to be an open trace with no conductive path to ground.
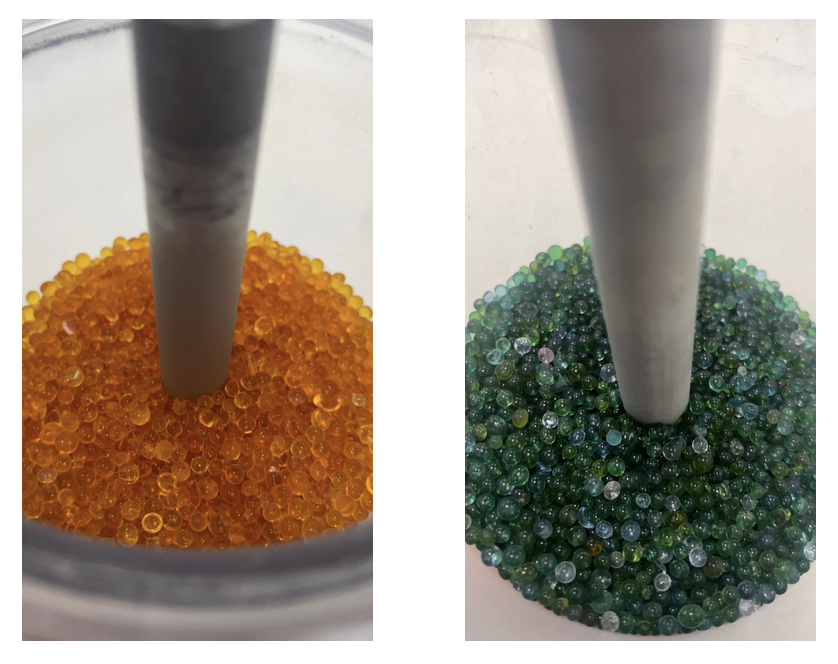
Desiccant Air Dryer
Keeps abrasive dry for consistent blasting. Silica gel desiccant beads absorb moisture to dew points as low as -25°F at flow rates up to 7.5 SCFM. Color change beads turn from orange to green when it’s time to change them.
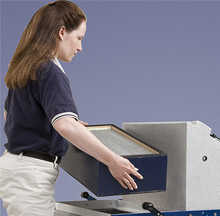
HEPA Filtration
A powerful dust collector with advanced downdraft technology, the ProCenter Plus comes equipped with an easy-to-replace HEPA filter. HEPA air filtration means 99.97% of all particles greater than 0.3 micron in size are removed for a clean work environment.
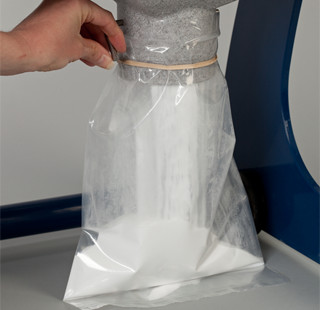
Maintenance in Minutes
Emptying spent powder from the hopper isn’t the usual mess found with most dust collectors. When cleaning is necessary, removal of spent abrasive is quick and easy with a half-turn of a butterfly valve at the bottom of the hopper.
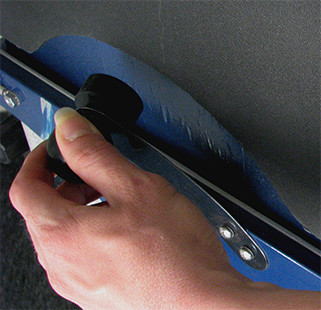
Filter Mallet
The filter mallets allow the operator to quickly knock off spent abrasive that accumulates on the underside of the HEPA filter. Regular use of the filter mallets maintains air flow in the work chamber.
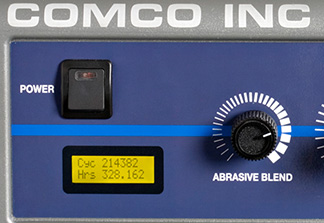
Simple Tracking
The easy-to-read LCD display tracks blast cycles and hours, providing clear milestones for maintenance.
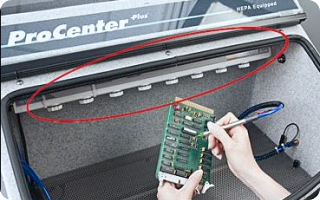
The Ionizer Bar
Floods the entire work chamber with ionized air to neutralize static build-up. Built-in sensors monitor the effectiveness of the ion flow and indicator lights alert the operator to any changes in operation.

Grounded Handpiece
Works with the conductive nozzle to provide a conduit for static, sending it straight to the grounding jacks instead of onto a PCB.

Conductive Nozzle
Limits the potential for a charge to travel to the board from the abrasive hose. A conductive nozzle also blocks a charge that could arc from the operator. Should be used with the grounded handpiece.
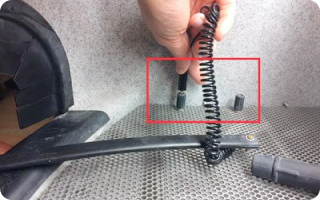
Grounding Jacks
Provide convenient connection points for a wrist-stat, the edge grounding bar, and the needle probe.

Edge Conductor Grounding Bar
Grounds all edge pins on boards that have edge connectors. This bar is made of conductive rubber material and connects to a grounding jack on the floor of the ProCenter Plus.

Needle Probe
Pierces through the coating and grounds a target trace when the defect is known to be an open trace with no conductive path to ground.
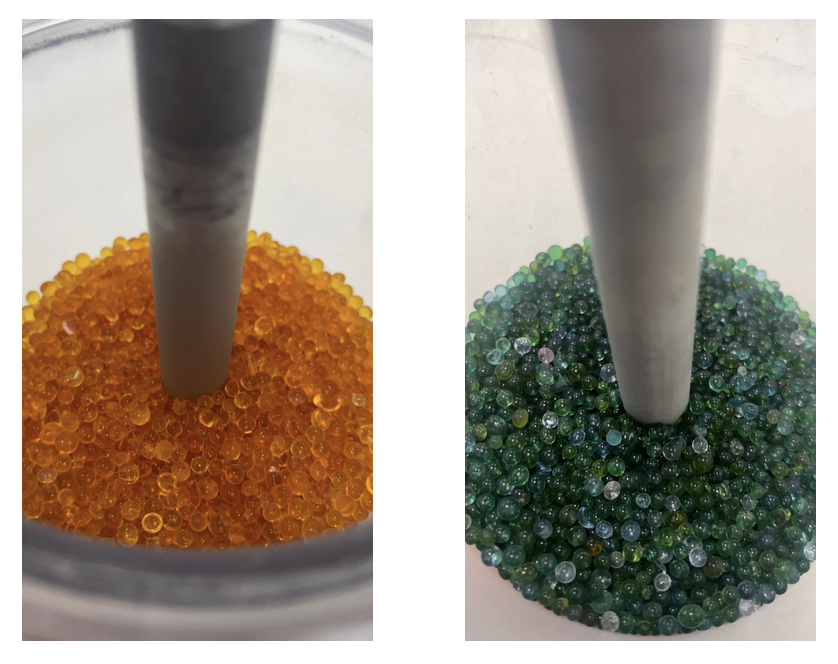
Desiccant Air Dryer
Keeps abrasive dry for consistent blasting. Silica gel desiccant beads absorb moisture to dew points as low as -25°F at flow rates up to 7.5 SCFM. Color change beads turn from orange to green when it’s time to change them.
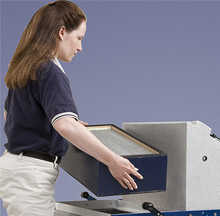
HEPA Filtration
A powerful dust collector with advanced downdraft technology, the ProCenter Plus comes equipped with an easy-to-replace HEPA filter. HEPA air filtration means 99.97% of all particles greater than 0.3 micron in size are removed for a clean work environment.
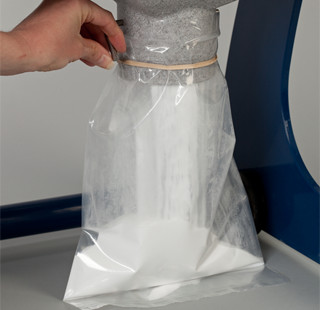
Maintenance in Minutes
Emptying spent powder from the hopper isn’t the usual mess found with most dust collectors. When cleaning is necessary, removal of spent abrasive is quick and easy with a half-turn of a butterfly valve at the bottom of the hopper.
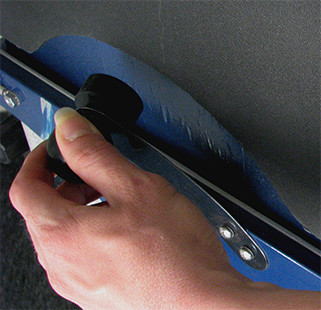
Filter Mallet
The filter mallets allow the operator to quickly knock off spent abrasive that accumulates on the underside of the HEPA filter. Regular use of the filter mallets maintains air flow in the work chamber.
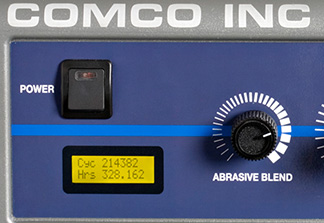
Simple Tracking
The easy-to-read LCD display tracks blast cycles and hours, providing clear milestones for maintenance.
Features
ProCenter Plus™ and AccuFlo®
Air Filter Efficiency: 99.97%
Sound Level: 68 dBA
Air Flow: 500 SCFM
$500 Off
Exclusive Offer
Mention code “CCR” in your message for $500 off of your ProCenterPlus ESD and AccuFlo package.
Send Us Your Sample Part!
MicroBlasting’s benefits can be a bit of a mystery. Our applications engineers have the experience and complete test facilities to process your parts. If you think MicroBlasting may be appropriate for your application, our team would love the opportunity to help you out.