MicroBlasting Technologies for Electronic Components
Micro-precision sandblasting is deceptively simple. Unlike traditional sandblasting, this process uses very fine media, small nozzles, and a consistent abrasive feed to deliver a tool with a laser-beam focus and exacting precision. Clean, strip, texture, etch and deburr delicate surfaces without causing dimensional changes to part geometry.
Your Partner for Electronic Component Solutions.
We’ll work closely with you by applying our engineering skills to your problem, providing the process with our technologies, and sharing our accumulated expertise to develop solutions that are efficient and cost effective.
-
Applied Engineering with a Deep Understanding of Electronic Components
Engineering is at the core of Comco. Our engineers have a background in the medical, aerospace, and semiconductor industries. While we are experts at MicroBlasting, we can also “speak your language.”
-
Providing the process at no additional cost to you
Let us prove how a custom MicroBlasting process would work for you while sharing our engineering expertise up front, without charge.
-
Sharing our skills & knowledge throughout our partnership
We’ll share our engineering skills and knowledge at every step of our partnership. Advanced technical support continues beyond your initial purchase of our MicroBlasting systems, and we also offer assistance with new applications as they arise.
Delineation
0.007″
Create a consistent surface finish with a 0.007″ delineation between blasted and unblasted regions.
Depth Control
70 nm
Etch channels for microfluidics with precise depth control.
Surface Finish
0.13 – 3.8 micron
Control the Ra and Sdr of your finish within 10%
What can be achieved with MicroBlasting?
MicroBlasting is an effective solution for electronics industry applications including conformal coating removal, decapping ICs, deburring PGAs and wave guides, texturing flex circuitry and removing excess epoxy from probe rings.
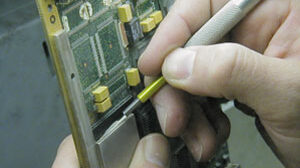
Conformal Coating Removal
Selectively remove conformal coating from printed circuit boards without damage to the board.
Read More
Semiconductor Devices
Remove microns of surface material, create a sloped edge, without vibration or micro-cracking.
Read More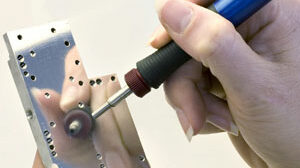
Wave Guides
Remove fine burrs from edges and openings of complex wave guide components without introducing dimensional changes or radiuses.
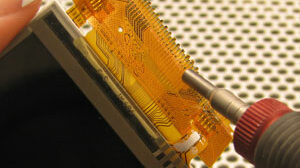
Flex Circuitry
Delicately texture the surface of rigid and flexible substrate materials to improve the bond, increasing the peel strength of the material when it is attached to other substrates.
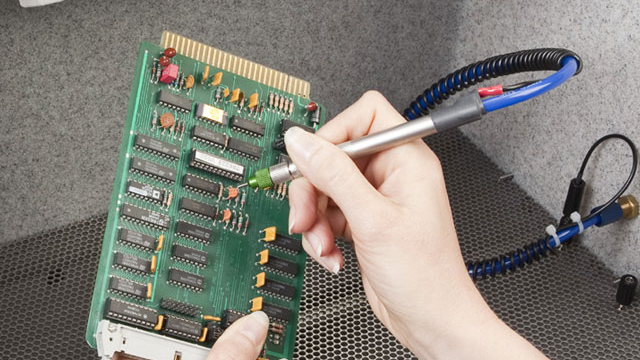
Brittle vs. Ductile
The coating removal process uses the abrasive qualities of MicroBlasting to carefully erode layers of unwanted material from a base substrate. The process takes advantage of the different physical properties of the two layers. Brittle materials can be removed from soft ductile layers, or soft ductile layers can be removed from brittle layers.
Read more
Static Sensitive Application
You might think micro-precision sandblasting, or MicroBlasting, is an unlikely tool for coating removal on static sensitive circuit boards and electronics. You might expect all that dry air and abrasive to kick up a spark, create a mess, or mar delicate compositions. However, with the right adaptation to your equipment, you can greatly reduce the risks associated with ESD. MicroBlasting provides a gentle, precise and controllable approach to selectively remove parylene, epoxy, polyurethane, silicone, acrylic and more without danger.
Read more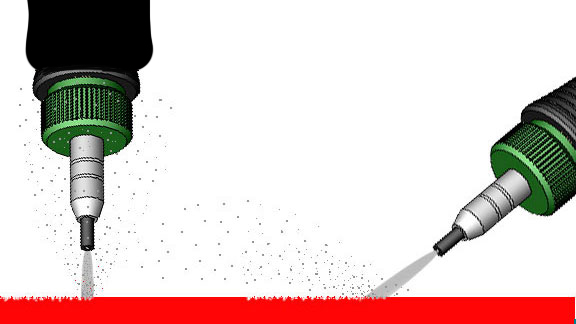
Nozzle Angle
Abrasive particles transfer the most impact energy when the nozzle is positioned at 90° to the target, but abrasive particles ricochet at this direct angle, crowding and slowing the stream. When cleaning or eroding surface material, hold the nozzle at or near a 75° angle to the target.
Read MoreThe Manual System
The AccuFlo® produces a steady flow of abrasive which ensures consistent results. It processes parts faster than most traditional micro-abrasive blasters, and it does so with greater powder efficiency. The AccuFlo is able to handle a wide-range of abrasives and suits most MicroBlasting applications.
Learn moreAutomated Solutions
When a manual MicroBlasting system cannot provide the output or meet your tolerance requirements; Comco’s automated systems deliver all the benefits of a manual system with greater precision and efficiency. Both the Advanced Lathe and the JetCenter are designed for the steady processing of precision parts. Each automated system is customizable from a proven platform and delivered as a turnkey solution.
Learn moreWhy Choose Comco?
Do you know what sets a Comco micro-precision sandblaster apart from others? In short, It’s our modulator. This pulsing heart of our system transforms the technology from a dirt sprayer into a precision tool.
Learn moreReady to Start MicroBlasting?
Contact Us
A Complete MicroBlasting Solution
Comfortable
Ergonomic design reduces operator fatigue
Versatile
Flows a wide range of media
Consistent
Unique patented modulated abrasive feed
User Friendly
Easy to set-up and easy to maintain
Mobile
Casters allow for adaptive cell environments
Clean & Quiet
HEPA filtration and customized fan box improves operation
Cost-effective
Our best for a turnkey solution
Customizable
Offers a range of workholding and blast head options
Scalable
Designed to grow from manual to fully automatic
User Friendly
Intuitive user interface for programming and operation
Turnkey
Delivered production ready
Peace of mind
Fully documented and supported
Consistent
Unique patented modulated abrasive feed
Robust
Stable in full production
Your Privacy and Security are Our Priority
-
Our Commitment to Privacy
We are committed to protecting our clients. That’s why we take your highly specialized, confidential projects seriously.
-
Trusted Partners
Great customer relationships begin with trust. We are dedicated to protecting our clients’ confidential R&D sample parts and data.
-
Learn More
Contact us to learn more about how we follow the highest standards to protect your business data.
TRY OUR PROCESS
See what precision MicroBlasting can do for you. Send us a part and we’ll MicroBlast it, analyze it, and return it to you with a detailed report.
Schedule a Demo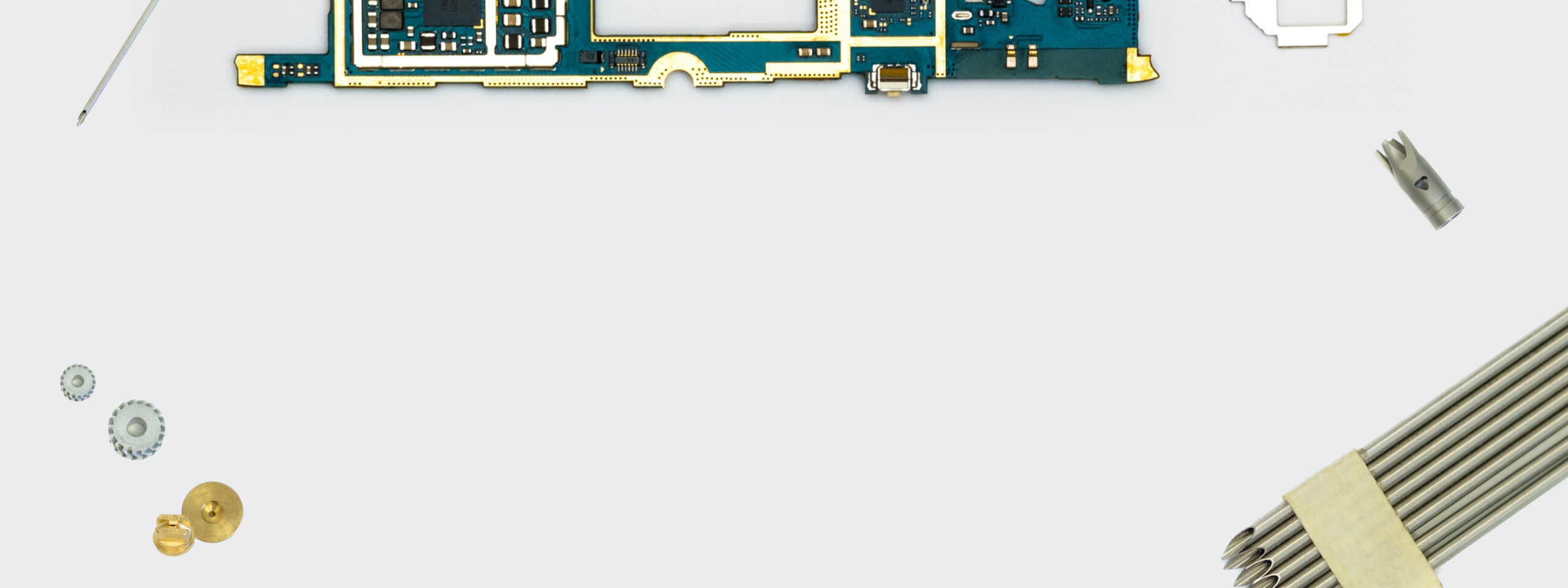