What is MicroBlasting?
MicroBlasting, or sandblasting on a micro-scale, is one of the most versatile surface alteration and material removal methods available. By simply adjusting the blast pressure, abrasive or nozzle, a Comco blaster easily turns from a tool that cuts vias in silicon wafers into a tool that deburrs the heal of stainless steel needles or a tool that textures bone screws.
Unfamiliar with MicroBlasting?
Are small imperfections getting in the way of your big idea? MicroBlasting is specifically designed to benefit small, intricate, and high-value parts. Unlike traditional sandblasting, MicroBlasting uses high velocity, micron-sized abrasives that can target and remove microns of material. The result is a reliable and repeatable method for deburring, texturing, cleaning, stripping, etching or milling part surfaces.
Solutions for Every Application
Surface Texturing
Engineering surface finishes for integration.
Dental Implants
Texturing a dental implant accelerates osseo-integration.
Ceramic Wafers
Texture the surface of a silicon wafer to improve light absorption and decrease reflection.
Multi-axis Load Cells
MicroBlasting is used to cut through the black anodize and texture the surface to improve the bond with flex circuitry.
Coating Removal
Remove coatings without damaging the underlying part.
Pacemaker Headers
Remove excess encapsulation that seeps out from the header during installation.
Reconditioning Turbine Blades
Refurbish either land-based gas or jet-engine turbines by removing the protective oxide layer.
Metalization on ceramic components
Remove metalization on ceramic components to improve electrical isolation.
Precision Deburring
Remove fine feather burrs without dimensional changes.
Polymers
Certain softer abrasives, like Sodium Bicarbonate, remove burrs quickly without damaging the underlying surface.
Bone Screws
Remove burrs while maintaining a sharp cutting edge. Can also create a compressive layer on the surface of the threads, which helps to improve the fatigue life.
Metals
Titanium hardens as it heats up, making it tough to machine. MicroBlasting with glass bead gently removes burrs without changing part geometry.
Abrasive Jet Machining
Drill holes, cut slots without generating heat nor vibration.
Lens Engraving
Etch serial numbers into lenses for ring laser gyros without creating micro-cracks. rnrn
Hydrodynamic seals
Etch shallow channels into the groves or channels of the surface of a seal to crate an air bearing.
Thermocouples
Remove MgO to expose contacts for bonding on heat-sensing harnesses.
MicroBlasting is effective on a wide range of materials.
Browse Materials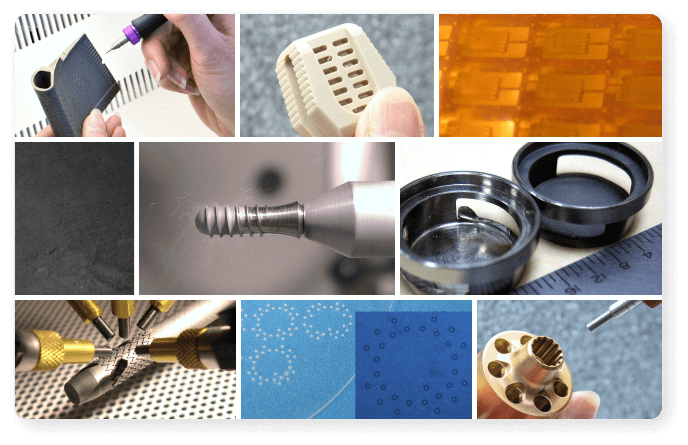
Materials We’ve Worked With
MicroBlasting is used on a variety of materials and compositions, thanks in part to the wide range of abrasive media available. We often work with the following materials used by the medical, aerospace, automotive, semiconductor and power systems industries. Can’t find what you’re looking for? Contact us and we’ll let you know how your material(s) can be used with our MicroBlasting technologies.

Aluminum
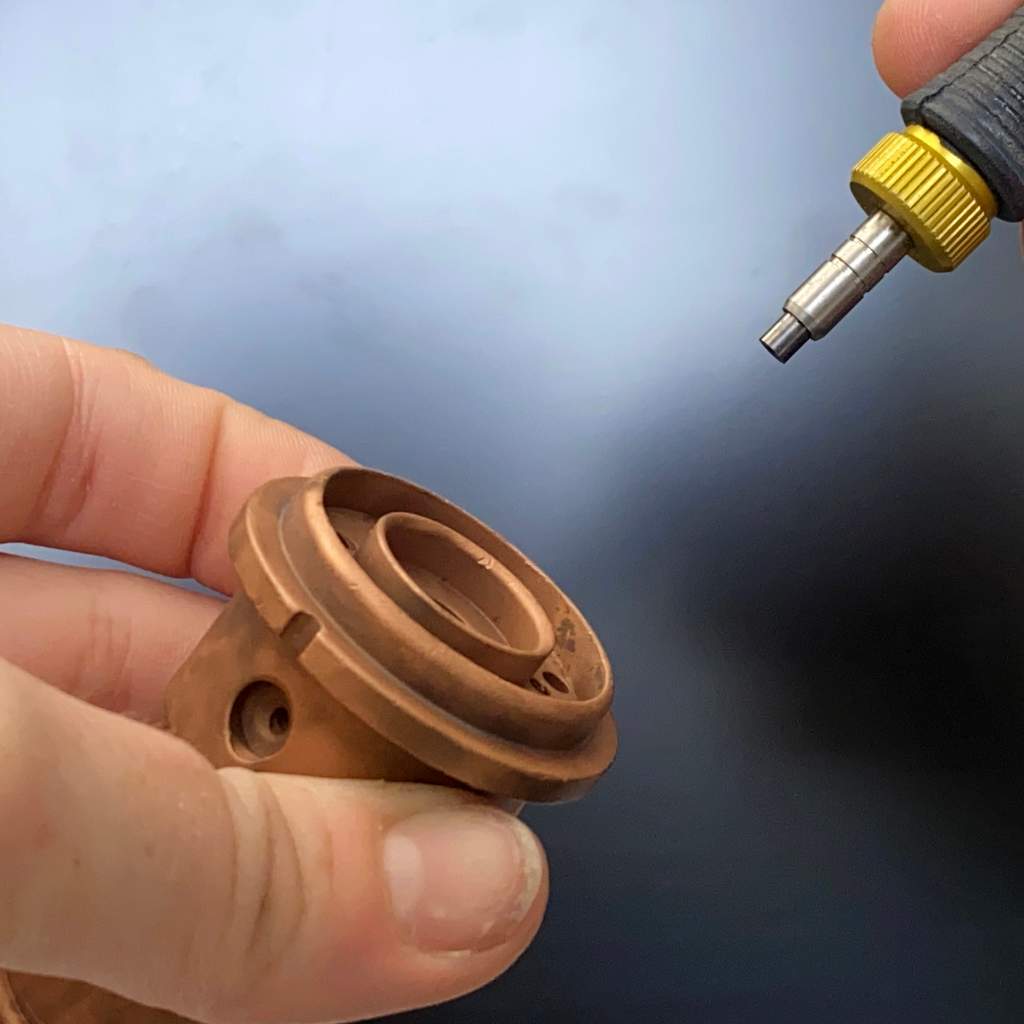
Bronze

Copper

Ceramic

Glass

Graphite

Inconel
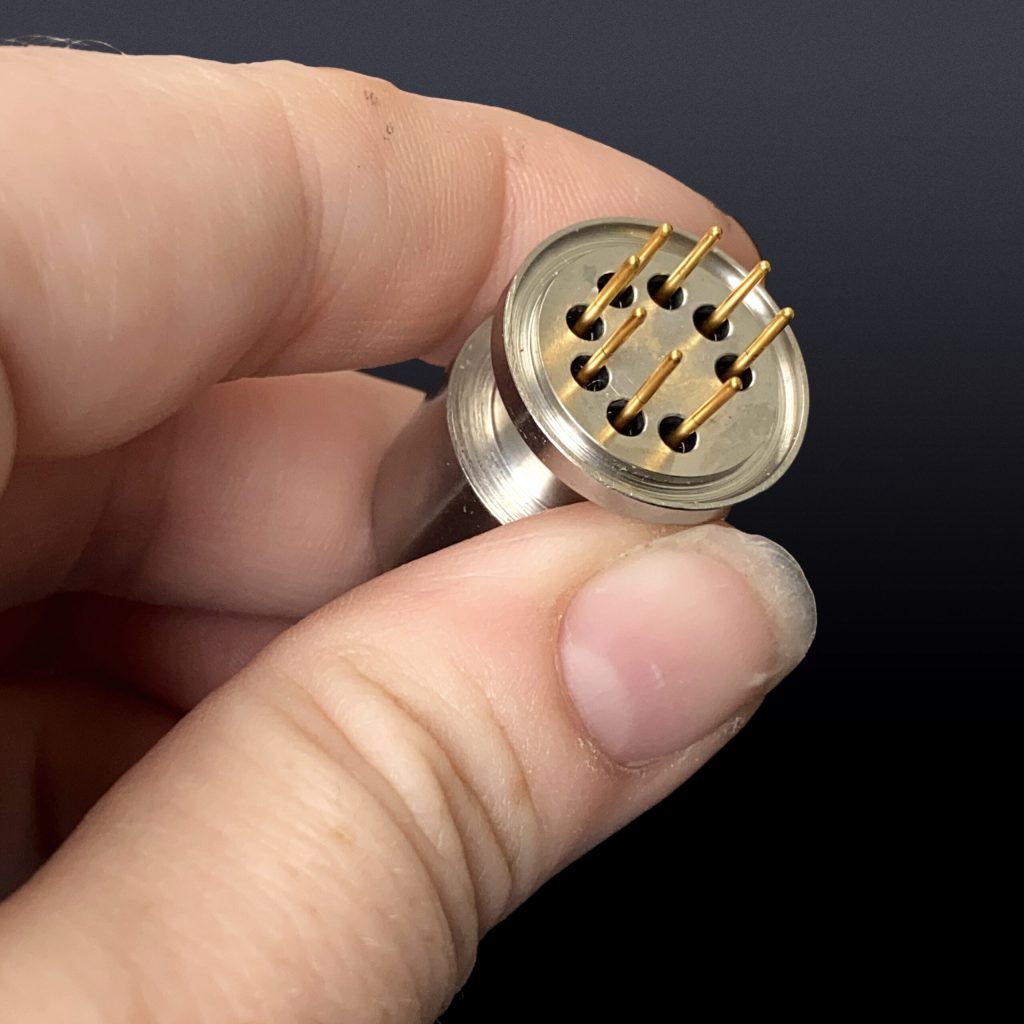
Kovar

Nitinol

Polypropylene

PEEK
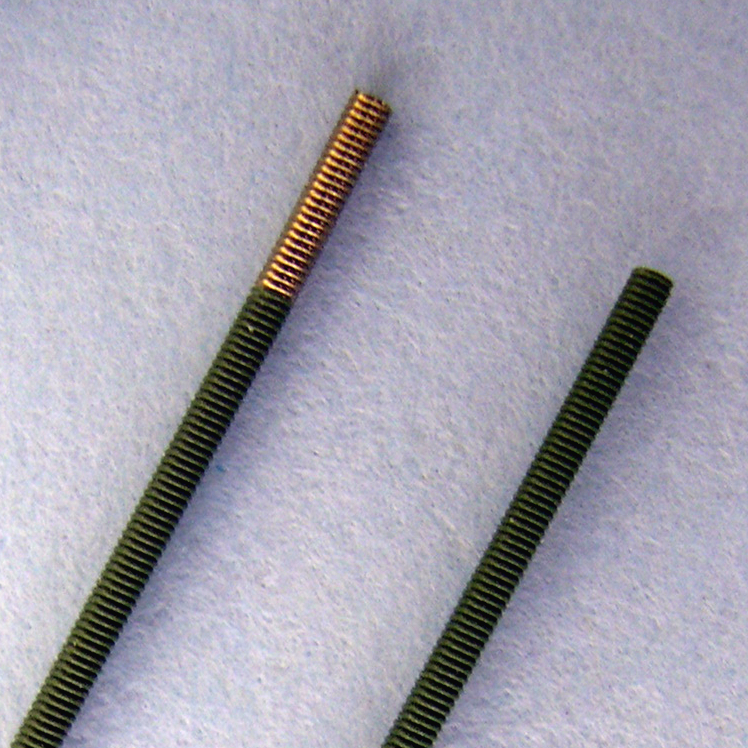
PTFE
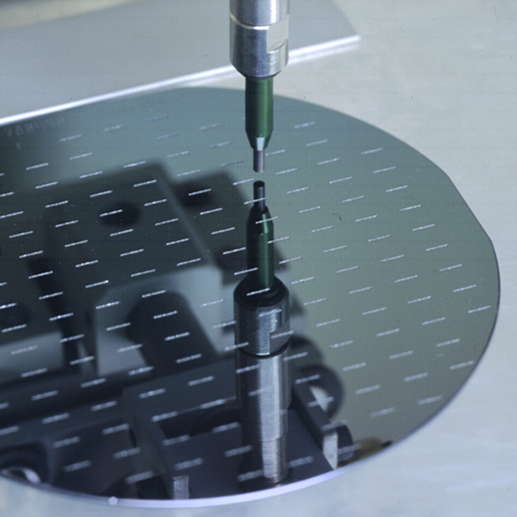
Silicon

Stainless Steel

Titanium

Brass
A Complete MicroBlasting Solution
Comfortable
Ergonomic design reduces operator fatigue
Versatile
Flows a wide range of media
Consistent
Unique patented modulated abrasive feed
User Friendly
Easy to set-up and easy to maintain
Mobile
Casters allow for adaptive cell environments
Clean & Quiet
HEPA filtration and customized fan box improves operation
Cost-effective
Our best for a turnkey solution
Customizable
Offers a range of workholding and blast head options
Scalable
Designed to grow from manual to fully automatic
User Friendly
Intuitive user interface for programming and operation
Turnkey
Delivered production ready
Peace of mind
Fully documented and supported
Consistent
Unique patented modulated abrasive feed
Robust
Stable in full production
Your Partner for Industrial Engineering Solutions.
We’ll work closely with you by applying our engineering skills to your problem, providing the process with our technologies, and sharing our accumulated expertise to develop solutions that are efficient and cost effective.
-
Applied Engineering with a Deep Understanding of Manufacturing Processes
Engineering is at the core of Comco. Our engineers have a background in the medical, aerospace, and semiconductor industries. While we are experts at MicroBlasting, we can also “speak your language.”
-
Providing the process at no additional cost to you
Let us prove how a custom MicroBlasting process would work for you while sharing our engineering expertise up front, without charge.
-
Sharing our skills & knowledge throughout our partnership
We’ll share our engineering skills and knowledge at every step of our partnership. Advanced technical support continues beyond your initial purchase of our MicroBlasting systems, and we also offer assistance with new applications as they arise.